By: Garry Gordon, MS, and Robert M. Traynor, Ed.D., MBA, F-NAP
Article first published in WorkPlace Material Handling & Safety, Nov 2022.
The World Health Organization estimates that 1.5 billion people (nearly 20% of the global population) live with some degree of recordable hearing impairment.1 For 700 million of these individuals, their degree of hearing impairment is considered a disability.
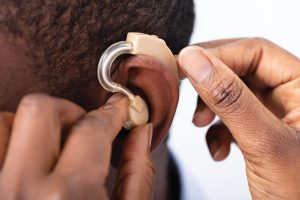
© Andrey Popov – stock.adobe.com
Hearing loss in the U.S. is the third most common chronic physical condition among adults, affecting 14% of the population – as many a 46 million individuals.2 The National Institute for Occupational Safety and Health (NIOSH) indicates that about 12% of the U.S. working population – or 26 million workers – are hearing impaired, with 24% caused by occupational noise exposure.3
For industrial employees with normal hearing or a mild hearing loss, the options for protection from hazardous occupational noise exposure are numerous. While there are no specific regulations that apply to the hearing impaired, workers are subject to the same occupational hearing conservation requirements as workers with normal hearing. If the worker has a moderate to severe hearing loss, hearing aid use is generally not allowed. These rules seriously restrict hearing-impaired workers for specific jobs and, ultimately, promotion and tenure within the company.
The Problem
The hearing impairment that causes problems at home follows the individual into the workplace. There is no specific guidance regarding the use of hearing aids in the workplace from OSHA, the Mine Safety and Health Administration (MSHA) or Federal Railroad Administration (FRA).
Most corporate hearing conservation programs (HCP), however, do not allow the use of hearing aids in hazardous noise areas. To comply with federal regulations, solid or foam earplugs and/or earmuffs are used as hearing protection devices (HPDs). Typically, these are designed to provide uniform attenuation (reduction) of sound at all frequencies and reduce more energy for high frequency sounds, the exact area where speech resides. The use of this uniform reduction of the sound attenuation only complicates the problem for workers with moderate to severe hearing loss. The use of these devices with uniform sound attenuation provides an increased hearing loss to those who are hearing impaired.
Attempts to use hearing aids have also been hampered in that most devices are coupled into the ear canal with an earmold that has an opening into the atmosphere, called a vent, and even more commonly, fit with a tip called an open dome (allows for no plugging or occlusion of the ear). Both vents and open domes couple the hearing aid to the ear canal, minimizing the echoing issues caused by plugging the ear. Unfortunately, these hearing aid fittings allow sound into the canal through the venting or open dome and do not provide protective plugging of the ear canal unless worn under an earmuff.
In most corporate HCPs, concerns about the use of hearing aids in these hazardous noise areas have been due to the poor performance of traditional hearing aids:
- – Difficulty understanding speech or discerning environmental sounds increase when the ambient (background) noise level has a similar pitch to the sounds of speech
- – Difficulty in hearing instructions clearly, perceiving alarm signals or locating the source of the sound
- – Difficulty detecting changes in machinery noise that will indicate either normal operation or a malfunction
- – Hearing aids are designed to maximize speech perception generally in semi-quiet environments, specifically focusing on to speech directed to the individual from the front rather than from all around them
- – Echoes may cause problems determining the direction and distance of sounds
- – Overamplification of specific frequencies (pitches) that may aggravate the hearing loss and create an even more hazardous situation
For these reasons, restrictions on the use of older technology hearing aids were likely well founded. Thus, the proverbial Catch 22 dilemma: the worker has a hearing loss and cannot use traditional hearing protection devices (HPDs), but OSHA4, MSHA5 and FRA6 mandate HPDs anytime the noise levels reach a time weighted average (TWA) of 90 dBA or higher or a TWA of 85 dBA if the worker has experienced a standard threshold shift (worsening of their hearing). Consequently, hearing aids are removed and HPDs are inserted when hearing impaired workers are in hazardous noise areas, compromising the safety of the worker and others in the hazardous noise environment.
Today’s technology offers dual purpose hearing aids that can be programmed to amplify specific hearing losses as well as provide hearing protection to the individual user. For example, a worker may now have a hearing program for normal situations in Memory 1 while simultaneously having a hazardous noise exposure program in Memory 2. The use of computerized multi-memories and programming have totally changed the scheme for how to use hearing aids in the workplace. While the worker may need to change to a solid coupling to the ear, the device will compensate with protection for the hazardous noise. A contemporary hearing aid may be beneficial for both general environments and the workplace.
Future of Multifunction Hearing Aids
It is difficult to understand why most major hearing aid manufacturers have not become involved in industrial and recreational markets. While clinical markets are their main customers, the technical viability of their products for provision of hearing protection in these markets would benefit to an unserved population. The advancement of hearing aid technology has progressed substantially in just a few short years. For workers with hearing loss, using their hearing aids on the job allows:
- – Better communication among the workers and supervisory personnel, facilitating a more efficient workplace.
- – Improved safety because workers are more aware of alarms and warning signals
- – Monitoring of equipment and/or the workplace environment for changes in the manufacturing processes or possible breakdowns
Once commonplace, multifunction hearing aids can now be provided by various third-party insurance provider networks as part of the current insurance programs now offered by companies. The benefits of a third-party provided multifunction hearing device include improved safety, better situational awareness and much happier cadre of hearing-impaired employees.
References:
- – WHO World Report on Hearing, March 2021.
- – ASHA (2017). Hearing Loss Prevalence Declines. ASHA Leader, Vol 22, No 3. Retrieved October 1, 2022.
- – NIOSH (2021). Occupational Hearing Loss Surveillance. Retrieved October 1, 2022.
- – OSHA Noise Regulation, 29 CFR 1910.95. Hearing Conservation Amendment; Final Rule, March 1983.
- – MSHA Noise Regulation 30 CFR Part 62: Occupational noise Exposure, September 13, 2000
- – FRA Rule 49, CFR 227 and 229: Final Rule on Occupational Noise Exposures for Railroad Operating Employees, February 26, 2007
About the Authors
Robert M. Traynor, Ed.D., MBA, FNAP, is an Adjunct Professor of Audiology at the University of Arkansas for Medical Sciences and Salus University and a Fellow of the National Academies of Practice. He also consults and does forensic audiology. https://roberttraynor.com
Garry Gordon, MS, is the CEO/Owner and Audiologist/Instructor at E.A.R Inc. Gordon has served well over 4,000 major medical, audiological and industrial accounts and trained a network of 500+ recreational and industrial providers who market high-quality hearing protection.
https://earinc.com